How Much Does It Cost to Manufacture One Rupee Coin?
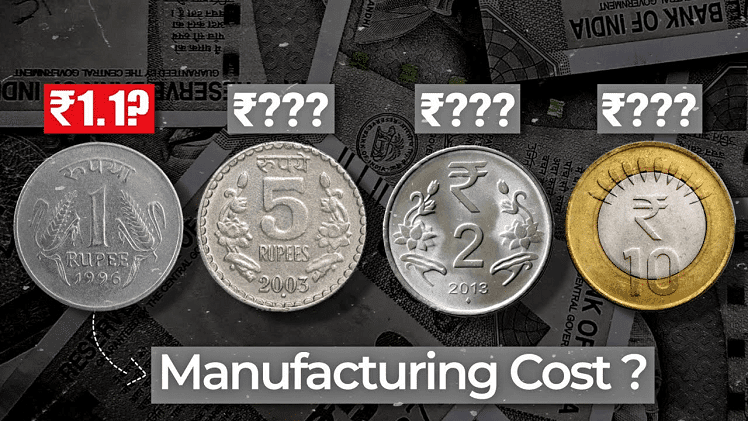
The cost of producing currency is a topic that sparks curiosity. People often wonder how much effort and expense go into making even the smallest denominations, like the one rupee coin. It might seem like a simple metal piece, but crafting it involves various elements like raw materials, minting processes, labor, and logistical costs. Understanding the real manufacturing cost of a one rupee coin helps us appreciate the intricacies of currency production and how governments manage resources to keep economies stable. Let’s explore the entire process, from material selection to the final coin that lands in our pockets.
What Goes Into Manufacturing a One Rupee Coin?
Creating a one rupee coin isn’t just about melting metal and stamping it into shape. The process involves several stages that contribute to the overall cost. Raw materials form the base of this cost structure. Typically, one rupee coins are made from stainless steel or nickel-brass alloys, depending on the country’s minting policies. The price of these metals fluctuates in the global market, directly impacting the coin’s production cost.
After acquiring raw materials, the metals go through refining and rolling processes. Sheets of metal are flattened and cut into circular blanks. These blanks are carefully weighed and measured to ensure they match the coin’s standard specifications. Even minor discrepancies can cause the batch to be discarded, adding to production waste and increasing costs.
Once the blanks are ready, they move to the minting stage. Massive hydraulic presses stamp the coins with intricate designs, national emblems, and security features. Precision is critical here, as a faulty press can ruin hundreds of coins in seconds. After minting, each coin undergoes quality control checks to eliminate defective pieces. Even transporting the finished coins to banks and distribution centers adds logistical expenses, contributing to the final manufacturing cost.
The Real Cost of Producing One Rupee Coin
The actual cost of manufacturing a one rupee coin is often higher than its face value. Reports suggest that minting a single rupee coin can cost around 1.11 to 1.28 rupees, depending on material prices and production efficiency. This means the government spends more than the coin’s worth to keep it in circulation. It may sound inefficient, but physical currency remains essential for small transactions and supporting rural economies where digital payments aren’t always viable.
Materials account for the most significant chunk of production costs. Stainless steel, used in modern rupee coins, isn’t just chosen for durability — it resists corrosion and lasts longer in circulation. But the price of steel isn’t static, and global market shifts can quickly raise manufacturing expenses. Minting facilities also consume substantial amounts of energy, with high-powered machinery running constantly to produce millions of coins annually.
Labor and maintenance costs further add to the total. Skilled workers operate the machines, perform quality checks, and manage logistics. Maintaining the minting equipment, which wears out under continuous use, requires regular investment. Despite these expenses, governments continue producing low-denomination coins because they facilitate small-scale commerce and remain vital to everyday transactions.
Why Governments Still Produce One Rupee Coins Despite Higher Costs
It might seem impractical to produce coins at a loss, but governments continue minting low-value currency for several reasons. First, coins have longer lifespans than paper currency. While banknotes wear out within a few years, coins can last decades. Over time, this longevity offsets the higher initial manufacturing cost of rupee, making coins more cost-effective in the long run.
Another factor is accessibility. Coins are crucial for rural and low-income communities that rely on cash for daily transactions. In regions with limited access to digital payment systems, small change is essential for buying essentials, paying for transportation, and conducting minor business activities. Eliminating coins could disrupt local economies, causing more harm than the production losses themselves.
Symbolism also plays a role. National currency carries cultural and historical significance, with coins often featuring important figures, landmarks, and emblems. Removing a denomination might be perceived as a step back, especially in countries where physical cash remains an integral part of people’s lives. So, even if producing one rupee coins costs more than their face value, the broader economic and social benefits justify the expense.
The Future of Small Denomination Coins
As digital payments rise globally, many wonder whether small denomination coins will eventually disappear. Countries like Sweden and Denmark have already reduced their reliance on physical currency, and similar transitions are happening elsewhere. Yet, the complete elimination of coins is unlikely in the near future, especially in developing nations where cash usage remains high.
Governments may explore cost-cutting measures instead. Using cheaper metals, optimizing minting processes, and recycling old coins are potential strategies to reduce manufacturing expenses. Some countries have already switched to lower-cost alloys for their smaller coins, balancing durability with affordability. Others are investing in advanced minting technologies that minimize waste and energy consumption.
Despite technological advancements, coins are likely to endure as long as physical cash holds value in people’s lives. While digital payments are convenient, not everyone has access to smartphones, banking services, or reliable internet connections. For these populations, coins and small notes remain a lifeline, preserving their ability to participate in the economy without barriers.
Final Thought
Understanding the cost of manufacturing a one rupee coin reveals the complex logistics behind currency production. It’s not just about creating money — it’s about balancing economic efficiency with public accessibility. Even if minting small denomination coins results in short-term losses, the long-term benefits of maintaining cash-based transactions in certain regions make the expense worthwhile.
Coins may be small, but their impact is enormous. They enable countless daily transactions, support local businesses, and connect people to the financial system. While digital technology evolves, coins remain a tangible, trusted symbol of value that people worldwide continue to rely on. For now, the humble one rupee coin is here to stay — a reminder that sometimes, the simplest things are the most essential.
FAQ
Q: What is the current cost to manufacture one rupee coin in 2025?
A: The cost ranges between 1.11 to 1.28 rupees, depending on material and production factors.
Q: Why does it cost more to make a coin than its value?
A: Material costs, energy consumption, labor, and logistics all contribute to production expenses.
Q: Will one rupee coins ever be discontinued?
A: It’s unlikely in the near future, as coins are still vital for cash-based transactions, especially in rural areas.
Q: Are governments trying to reduce coin production costs?
A: Yes, many governments are exploring cheaper materials, better minting technologies, and coin recycling methods.